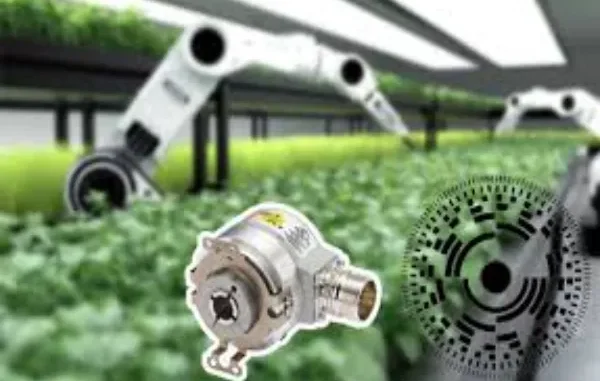
At the heart of precise motion control lies the encoder, a transducer that translates mechanical movement into a quantifiable electrical signal. This conversion is crucial for feedback control systems, enabling precise positioning and movement in various applications. Encoders come in multiple forms, with rotary encoders measuring rotational movement and linear encoders tracking linear displacement.
Among these, absolute encoders stand out. Unlike their incremental counterparts, which merely register changes in position, absolute encoders provide an unequivocal position reading for every shaft rotation. This unique characteristic stems from their ability to assign a distinct, non-repeating code to each position. This eliminates the need for homing routines after power interruptions, a significant advantage in many applications.
It is impossible to exaggerate the significance of absolute encoders. They are essential in contemporary robotics, where accurate joint placement is crucial. Motion control systems provide precise and seamless motions in various applications, from high-speed packaging lines to CNC machines. Absolute encoders are essential to industrial automation for process control, material handling, and robotic assembly.
They have numerous advantages. The direct position readout ensures high accuracy by removing the error accumulating that is typical of incremental systems. The absence of position loss during power outages increases reliability, reduces downtime, and boosts system performance. Lastly, engineers and system integrators favor them because of their ease of use, streamlining system integration and cutting down on development time.
Eltra Absolute Rotary Encoders represents the ultimate in this technology. Eltra encoders, well-known for their remarkable precision, durability, and adaptability, offer dependable position feedback in even the most taxing settings. Engineers and system integrators worldwide choose them because of their creative designs and cutting-edge production techniques, guaranteeing excellent performance and long-term durability.
By incorporating Eltra Absolute Rotary Encoders, engineers can achieve superior levels of precision and reliability in their motion control systems, unlocking new possibilities in robotics, automation, and beyond.
Working Principle of Absolute Encoders
A basic idea is at the core of absolute encoders: encoding each unique shaft position with a distinct digital code. This principle operates much like assigning a unique address to every house on a street. Each address provides an absolute location, allowing you to pinpoint any house without ambiguity. Similarly, an absolute encoder generates a unique digital code for every shaft position, enabling precise and unambiguous position feedback.
Common Technologies
One of the most prevalent technologies in absolute encoders is the optical encoder. These encoders utilize a precisely patterned code disc, typically etched with opaque and transparent segments. Light beams pass through the disc as the shaft rotates, and an array of photodetectors senses the varying light intensity. This pattern of light and dark translates into a unique digital code, representing the instantaneous shaft position. Optical encoders can be further categorized as single-turn, which measure a single revolution, or multi-turn, capable of tracking multiple shaft revolutions. While renowned for their high accuracy and resolution, optical encoders can be susceptible to environmental factors like dust, dirt, and vibrations.
Magnetic encoders offer a compelling alternative, leveraging the principles of magnetism to generate position data. A magnetic field, generated by a rotating magnet or a patterned magnetic strip, interacts with a series of sensors. The variations in the magnetic field strength are then translated into a digital position signal. Magnetic encoders exhibit exceptional robustness, demonstrating remarkable resistance to dirt, grime, and even harsh environmental conditions. However, their performance can be influenced by external magnetic fields, which may introduce inaccuracies.
Beyond optical and magnetic technologies, other approaches to absolute encoding exist. Capacitive encoders utilize changes in capacitance to determine position, while inductive encoders rely on variations in inductance. These technologies offer unique advantages, such as high resolution and immunity to certain environmental factors, and find specialized applications in various industries.
Key Components of an Absolute Encoder
An absolute encoder comprises several critical components that work in concert to provide precise position feedback.
At the core lies the shaft, the mechanical interface, transmitting rotational motion from the driven machine to the encoder. The shaft’s precision and rigidity are paramount to ensure accurate position sensing.
Attached to the shaft is the code disc, the heart of the absolute encoder. Typically made of glass or metal, this disc is precisely etched with a unique pattern of tracks or segments. This pattern, which can be encoded using schemes such as Gray code or binary code, represents the absolute position of the shaft. Gray code, with its inherent property of minimizing errors during transitions, is often favored in absolute encoders to ensure reliable position readings.
The read head interprets the information encoded on the code disc. In optical encoders, the read head employs a combination of light sources and photodetectors to detect the pattern of light and dark segments on the disc. In magnetic encoders, the read head utilizes magnetic sensors to detect the variations in the magnetic field generated by the rotating code disc.
Finally, the output interface determines how the encoder communicates the position data to the control system. Common interfaces include digital signals, parallel or serial communication protocols, and analog signals. Modern encoders often incorporate advanced communication protocols like fieldbus, enabling high-speed data transmission and seamless integration into complex control systems.
Advantages of Absolute Encoders
Absolute encoders are excellent at giving accurate and consistent position data, which is essential for maintaining the precision and dependability of contemporary motion control systems.
First, they are incredibly accurate due to their innate capacity to deliver a clear position readout for each shaft position. Absolute encoders give a more dependable and trustworthy position measurement by removing the uncertainty that comes with incremental encoders, which rely on counting pulses. Applications requiring precise positioning, such as robotics, CNC machining, and semiconductor production, depend heavily on this high accuracy.
The second important benefit is the ability to save position data even in the event of power outages or system resets. Absolute encoders maintain their last known position in contrast to incremental encoders, which stop tracking position when the power is cut off. This greatly speeds up system startup times and increases overall operational efficiency by doing away with the necessity for laborious homing operations.
Additionally, absolute encoders are made to be easily integrated. They often have a range of communication interfaces, including fieldbus, parallel, and serial protocols, allowing for easy integration into other control systems. This speeds up the time to market for new systems and products by streamlining system design and lowering integration efforts.
Lastly, smoother and more dependable motion control results from absolute encoders’ intrinsic benefits. Positioning mistakes are reduced, and accurate and consistent position feedback makes more precise control algorithms possible. This results in more production, better system performance, and higher-quality products.
Applications of Absolute Encoders
The versatility of absolute encoders shines through in a wide range of demanding applications across various industries.
- Robotics: In robotics, absolute encoders play a critical role in achieving precise and coordinated movements. They enable accurate joint position sensing, allowing robotic arms to execute intricate tasks with unparalleled precision. From delicate surgical procedures to complex manufacturing processes, absolute encoders empower robots to perform with enhanced dexterity and reliability.
- Motion Control Systems: Within motion control systems, absolute encoders are indispensable. CNC machines ensure precise tool positioning, creating complex and intricate parts with exceptional accuracy. In conveyor systems and packaging lines, they facilitate synchronized movement and precise product handling, optimizing production efficiency and minimizing downtime.
- Industrial Automation: Absolute encoders are instrumental in driving advancements in industrial automation. They enable precise control of factory automation systems, ensuring synchronized operation of various machinery and equipment. In process control applications, they provide critical feedback for optimizing production processes, improving product quality, and maximizing yield.
- Medical Equipment: The healthcare sector leverages absolute encoders to enhance the precision and safety of medical procedures. Surgical robotics enable surgeons to perform minimally invasive procedures with greater accuracy and control. Inpatient positioning systems ensure precise positioning and alignment, improving patient comfort and treatment outcomes.
- Aerospace: In the aerospace industry, absolute encoders contribute to critical flight control systems and positioning. They provide accurate and reliable position feedback for essential components like flight control surfaces, ensuring aircraft stability and maneuverability. In aircraft positioning systems, they enable precise alignment and docking procedures, enhancing safety and efficiency.
In conclusion, absolute encoders, which provide unmatched accuracy, dependability, and user-friendliness, constitute a significant breakthrough in motion control technology. They enable various applications, ranging from industrial automation and robotics to medical and aeronautical equipment, by offering clear position feedback for each shaft position. They are essential in today’s technologically advanced world because of their capacity to maintain position data even during power outages and their smooth integration into contemporary control systems.
Looking ahead, the future of absolute encoder technology holds immense promise. The goal of ongoing research and development is to push the limits of performance, focusing on lowering size and weight, improving robustness against environmental conditions, and reaching even higher resolutions. It is anticipated that new materials, sophisticated sensing systems, and creative design methodologies will surface, greatly enhancing the potential of absolute encoders. These developments will push motion control systems in various industries to new heights of accuracy and complexity, influencing automation and robotics in the future.
Leave a Reply